Solutions & Services
Ramentor – Services
With our solutions and services you can increase productivity, quality and cost-efficiency. By applying advanced RAMS methods and tools you achieve understanding about the complex and dynamic relations between failures and key performance indicators (KPI). With ELMAS and StockOptim we offer efficient simulation and analysis of dependability, and optimization of maintenance and spare part storage. This software family includes a wide variety of solutions for decreasing risk and improving overall efficiency.
Ramentor's expertise combines deep theoretical background of RAMS methods and tools with experience in challenging industrial risk assessment applications. Together with our customers we have analyzed RAMS and risks of, for example, paper and pulp mills, lifting equipment, data centers, pharmaceutical production lines, steel mills and processing lines, tyre production process, district cooling and heating plants, maintenance outsourcing, veneer production, propulsion equipment, nuclear plant, final disposal of spent nuclear fuel, particle accelerator, power transmission lines, material handling solutions and telecommunication networks. Cases have been made in design, realization and operation & maintenance stages to, for example, increase availability, decrease life-cycle costs, optimize maintenance plan, and assess the components' criticality.
Risk managementRisk management process and methods
Ramentor provides systematic risk management solutions for assessing the criticality of component failures and mitigating their overall effects. In the evolving operating environment it is necessary to perform risk management as a constant process. The enhanced process for recognizing and coping with the everyday risks is an essential asset for equipment manufacturers and process plants.
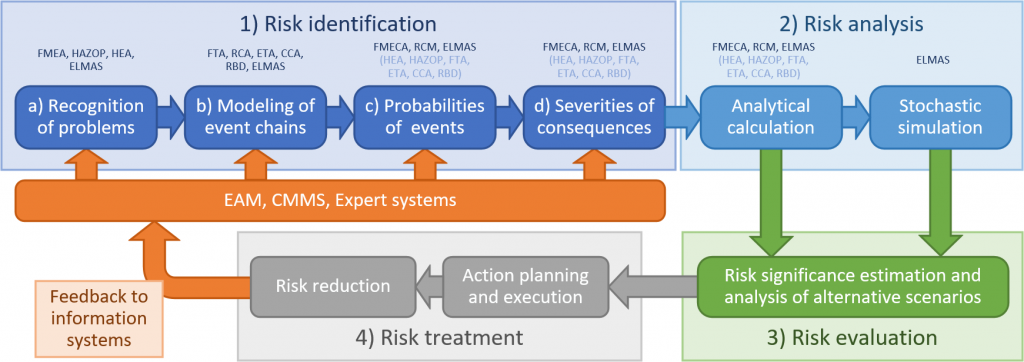
- ELMAS software provides a single user interface for various risk assessment tools. They support the methods for recognizing and managing the risks hiding in the operating environment. The risk management process contains following phases, which require different methods and tools:
- Risk identification
- Recognition of problems
- Modeling of event chains
- Estimating probabilities of events
- Estimating severities of consequences
- Risk analysis: Analytical calculation and stochastic simulation of risk
- Risk evaluation: Estimation of risk significance and analysis of alternative scenarios
- Risk treatment: Action planning and execution -> Risk reduction
Please ask for more information or quotation via reliability@afry.com
Expert services
Ramentor expert services
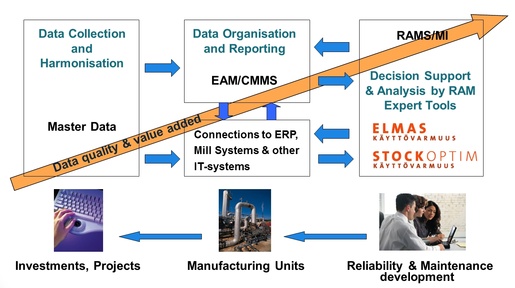
RAMS audit
- Value proposition for RAMS audit:
- The customer understands better the risks of the operational environment.
- The customer recognizes how the available RAMS information is currently capitalized and what is the potential of the information.
- The customer clarifies the perception about the critical parts of the production process.
- The customer receives an explicit plan for improving the RAMS in the most suitable manner.
- The content of the project:
- Preliminary study and planning (1-2 days)
- Workshop (1 day):
- Introduction to the operational environment, recognition of the risks and setting the goals
- Considering the quantity and quality of the currently available RAMS and cost information
- Finding the potential targets of the analysis (production, RAMS, costs, safety)
- Analyzing and reporting the collected information (1-3 days)
- Presenting the results (0.5 days):
- A review of the RAMS audit project phases
- Presenting the project report and the findings
- The project report:
- The report of the RAMS audit project includes:
- The recognized risks of the operational environment or the production unit
- The potential of capitalizing the currently available RAMS information
- The goals for the RAMS improvement, risk analysis and data collection
- A proposal for a customized RAMS training
- A proposal for the RAMS analysis of recognized problem:
- Project plan
- An estimation of amount of work
- An assessment of the improvement potential and an estimation of the time period when the RAMS analysis will pay off
RAMS analysis
- Value proposition for RAMS analysis:
- A made RAMS analysis will pay off at latest after three years, probably already during the first year.
- The RAMS analysis helps recognizing the most critical sub systems, components and failure modes.
- The actions recommended by the RAMS analysis enable improving RAMS cost-efficiently.
- The customer understands explicitly the risks of the operational environment.
- The customer has a knowledge for the most efficient capitalization of the available RAMS information.
- A systematic procedure is built for new RAMS analyses.
- The content of the project:
- Phases of a typical RAMS analysis project:
- Introduction to the analysis target and preliminary data collection
- Creation of the target's RAMS model by using ELMAS tool
- Failure, repair time and cost data collection from various sources ans inclusion of it in the RAMS model
- ELMAS simulation and analysis of results
- Action planning for the most critical failure modes
- Reporting the results and planning the continuous RAMS improvement procedure
- Meetings:
- Workshops: Data collection, action planning (5-15 days)
- Presenting the results: The project report and the findings (0.5 days)
- The report of the RAMS analysis project includes:
- A review of the analysis phases
- Results from the simulation: Reliability, availability and costs of the analysis target
- Classification (TOP 10 lists): The most critical sub systems, components and failure modes
- Risks and improvement potential of the analysis target
- Recommended actions and conclusions
ELMAS solutions
ELMAS risk management solutions
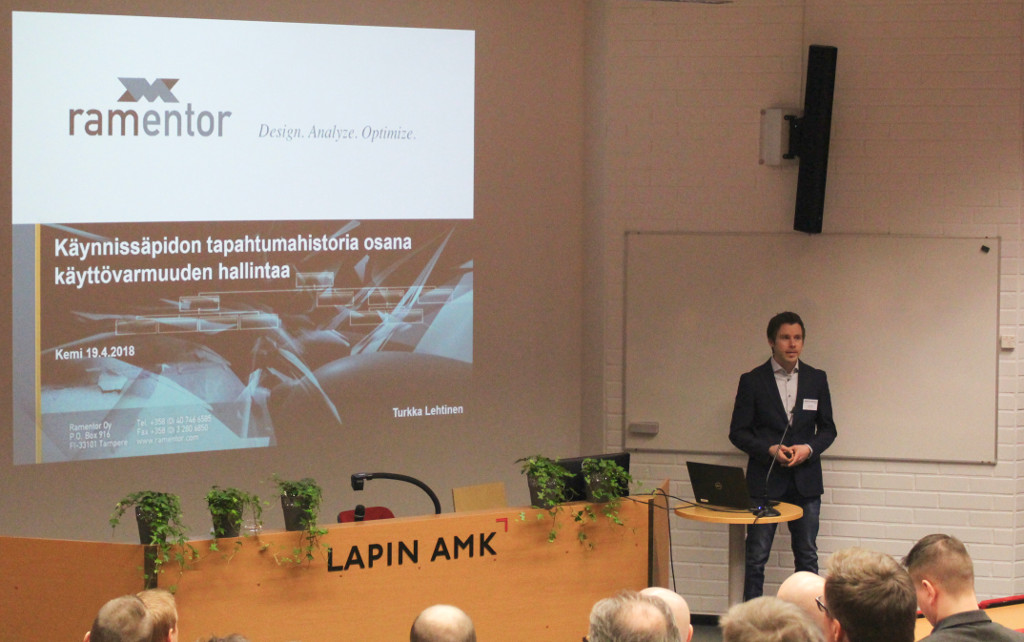
FTA – Fault Tree Analysis
Fault Tree Analysis (FTA) is a structured top-down method for the identification of causes, which lead to a system fault or other undesirable consequence. A fault tree is a graphical presentation of the logical links of component and subsystem failures that lead to an unwanted event. Quantitative FTA calculates explicit dependability parameters for the analyzed item.
- ELMAS software provides an efficient and intuitive graphical user interface for advanced FTA, which extends the traditional FTA method with various modelling features:
- Combine FTA with Reliability Block Diagram (RBD) and multi-state operation phase modelling
- Combine FTA with FMEA/FMECA and RCM
- Define stochastic relations and delays between events
- Define mode-dependent failure behaviors
- Include preventive maintenance actions
- Include Java-based scripts for definition of special rules and dynamic operation phases
LCC – Life-Cycle Cost
Life-Cycle Cost (LCC) includes all costs starting from the definition of the item to the moment of taking it off the use and wrecking or relocating it. Different costs can cumulate from manufacturing, use, education, maintenance and eventual end-of-life actions, and also indirectly from the downtime or losses caused by the item failures. Sophisticated LCC analysis should be performed as early as possible, as the majority of the costs will be determined based on the design decisions made in the start of the life-cycle.
- ELMAS software enables including the most common cost elements in a systematic LCC analysis:
- investment costs, acquisition price
- installation and order costs (including education)
- energy costs (predicted costs for the system use)
- usage costs (operations personnel costs)
- maintenance and repair costs (repeating and predictive repairs)
- downtime costs (lost production)
- environmental costs
- end-of-life costs
Criticality classification
Criticality classification can be applied for estimating the significance of the functions and the equipment in the system. Criticality classification produces important information to support the operations of maintenance, design and acquisition sections. Ramentor has included a criticality classification tool in the ELMAS software.
- Typically criticality classification directs these sections with the following methods:
- Creating suitable maintenance and inspection programs primarily for the most critical functions and equipment
- Equipment spare part criticalities are derived straight from the equipment criticalities
- Recognizing critical functions and equipment already in the design phase to inform and support the development process
- Provides information for the acquisition section about the requirements of the critical equipment
Read more about ELMAS Criticality classification (unfortunately available only in Finnish): ELMAS-Kriittisyysluokittelu.pdf
FMEA/FMECAFMEA/FMECA – Failure Mode and Effects (and Criticality) Analysis
Failure Mode and Effects Analysis (FMEA) is one of the first structured techniques for systematic failure analysis. FMEA can be extended to Failure Mode and Effects and Criticality Analysis (FMECA) by defining criticalities for the identified failure modes. Ramentor has included a FMEA/FMECA tool in the ELMAS software. This combination of FMEA/FMECA and several supporting modeling and simulation functions provides a novel perspective for applying the method.
- FMECA tries to answer the following questions:
- What can fail?
- What is the effect of the failure?
- How probable is the failure?
- What are the consequences of the failure?
- What can be done to the failure?
- How can the causes of the failure be removed?
- How can the severity of the failure be decreased?
- FMECA method can be applied, for example, to:
- make sure that all potential failure modes and their effects are taken into account to ensure undisturbed operation of the system
- recognize all the potential failure modes and to estimate the criticalities of their effects
- show the cause-consequence relations of each failure mode
- guide the selection between different design solutions and to choose the ones that have the most significant effect on relaibility and safety
- provide information for the maintenance planning
- provide information for quantitative reliability and dependability analysis
Read more about ELMAS FMEA (unfortunately available only in Finnish): ELMAS-FMEA.pdf
RCMRCM – Reliability Centered Maintenance
Ramentor has included a Reliability Centered Maintenance (RCM) tool in the ELMAS software for supporting an effective RCM that leads to improvements in maintenance operations. Together with the visual modeling and versatile simulation functions, ELMAS RCM is a flexible and user-friendly tool.
- The following list presents the seven basic questions that the RCM analysis aims to answer:
- What are the functions and performance standards of the object in its current operational environment?
- What will happen if the object fails (which functions will not be available)?
- What causes the lack or insufficiency of each function of the object?
- What happens when each failure occurs?
- What damages will each failure cause?
- What can be done to detect each failure early enough or to prevent it from happening?
- What must be done if a suitable preventive task cannot be found?
Read more about ELMAS RCM (unfortunately available only in Finnish) from a document that explains thoroughly how the RCM steps are performed with the ELMAS software in an effective and user-friendly manner: ELMAS-RCM.pdf
Internet of Things
Internet of Things (IoT)
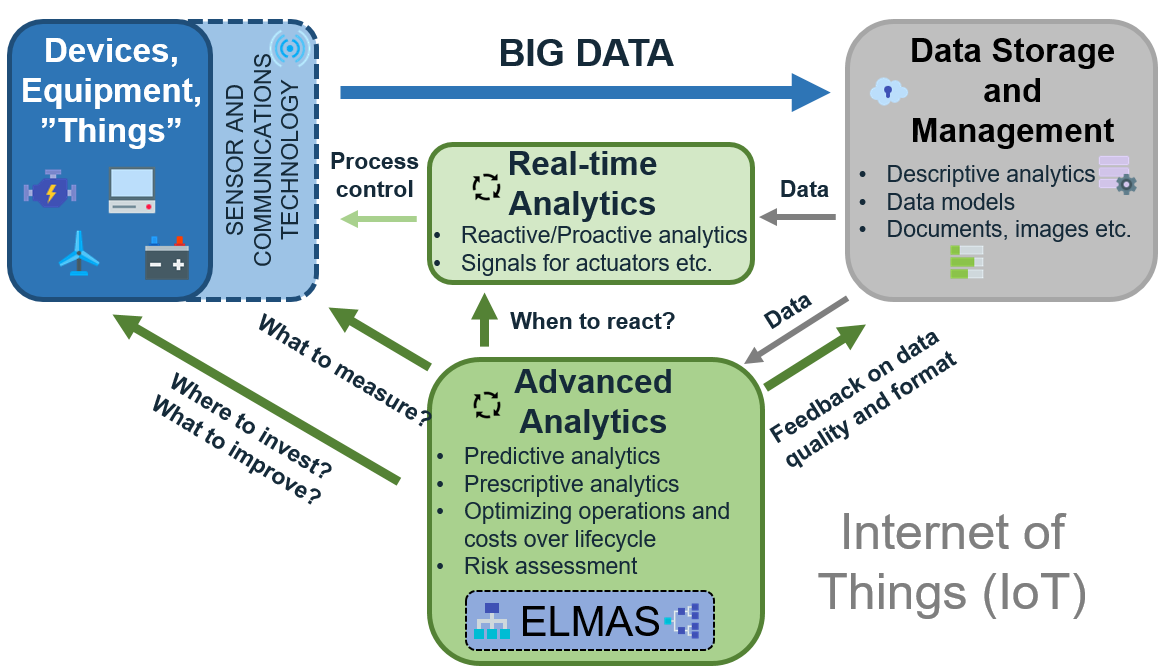
Creating basis for IoT
The startup phase of a new IoT system can take years until the system is properly defined and have collected enough event data to support all of the analytics. This phase of waiting for new data streams doesn’t though mean that advanced analytics can’t be applied. For example, ELMAS can use the already existing imperfect data with the help of local expert resources. This way it is possible to create the same improvement alternatives for the equipment as with the completed IoT systems, but in addition to this the analysis also provides important feedback for the ongoing IoT development.
With the results of ELMAS analysis it is for example possible to define which devices should be monitored to ensure the system operation and how much should be invested on the diagnostics on each device. Going through the old event history with the expert resources presents another major advantage by providing valuable information for the upcoming IIoT system. The information includes for example facts about the most problematic areas with the previous event data and gives understanding on what kind of data to collect in the future and in which form it should be transferred into the data storage.
All in all ELMAS brings more intelligence for the management and processing of the large data sets in the IIoT world. The analytics it provides allow to maintain and develop the reliability of the equipment and processes and therefore reducing the overall costs by improving the process efficiency. ELMAS software has a strong history in refining imperfect data to support the decision-making of Finnish industry organizations. The new data streams and the increased attention on data quality coming with the IIoT world further strengthens the possibilities ELMAS can provide for the development of operations.
AnalyticsAdvanced analytics
ELMAS is a modelling and simulation software specialized in reliability management and it operates in the field of advanced analytics when it comes to Industrial Internet of Things. Thanks to IIoT the amount and especially the quality of the collected data will be increasing and therefore significantly reducing the work effort required to use advanced analytics. Also ELMAS will benefit from the increased quality and accuracy of the available data as the need for reviewing the imperfect history data using various expert resources is no longer as critical as before.
Advanced analytics allow organizations to prepare for future events in a preventive manner (predictive analytics) and to create versatile calculation models for different improvement alternatives and use the results acquired from these calculations to develop the overall operations of the organization (prescriptive analytics). When operating with completed IoT systems ELMAS provides assistance in understanding the consequences of different equipment events and event chains for the operation of the whole system. The cause-consequence models describing the equipment operations are created into the software and they utilize the history event data collected into the data storage. By simulating the models together with the event data ELMAS can provide a clear view on the expectable future behavior of the equipment considering their reliability and life-cycle costs. This way the available raw data can be processed into important knowledge about the most significant equipment risks and used to create profitability calculations about different investment options considered for the equipment or the whole process.
StockOptim
StockOptim
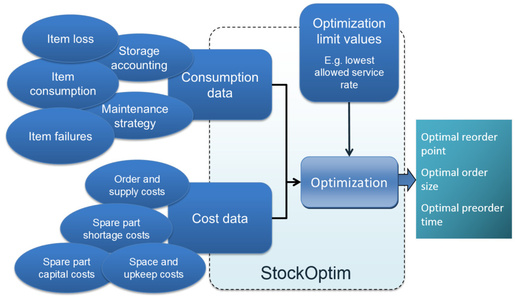
Spare part consumption modelling
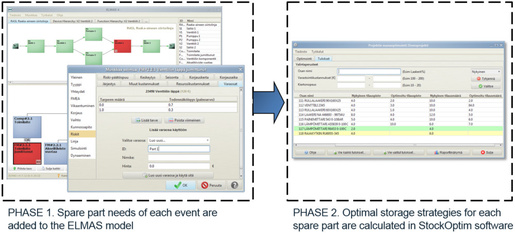
When defining the spare part consumption of a certain equipment entity it is possible to take advantage of an ELMAS model created of this entity. The root cause events (e.g. 'Pump X fails') in the ELMAS model can be inputted with a spare part consumption information that defines which spare parts are needed and with what probability, if the event is fulfilled. Normally the spare part need is defined to the root cause events of the model which makes it easier to define what spare parts are needed when the event comes true.
- Operations model:
- Creating an ELMAS model of the subsystem e.g. for a RAM analysis
- Defining the spare part needs for the root cause events in the ELMAS model
- Recognizing the critical events in the model with ELMAS software (event criticality defines the needed spare part criticalities)
- Simulating spare part consumption with ELMAS software
- Transferring the simulated consumption data to StockOptim software and inputting the rest of the required information for the optimization (i.e. item delivery time, purchase price and other common cost factors)
- Performing a StockOptim optimization for the item so that the storage requirement for the service rate equals the criticality of the event in the ELMAS model
- Going through the optimization results and checking unclear results with a more accurate simulation
- Taking into use the optimized storage strategies.
When performing the item optimization based on the ELMAS model it is important to check if the items consumed by the model have consumption also in some other locations excluded from the model. The consumption coming from these locations has to be added to StockOptim software so that the item storage strategy can be optimized with the true consumption data.
Mass optimization – Optimize your whole storage
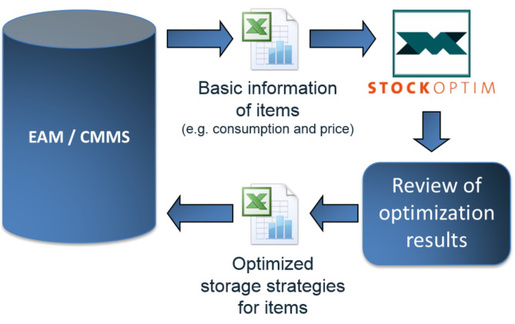
When companies are expanding their processes also the need for more spare parts arises. As a result of this the amount of stock items in the CMS grows easily very large, and so does the storaging costs. Cutting down these costs without affecting production has proven to be a challenging task to most.
StockOptim software allows the effective optimization of a large stock item groups that provides information about the possible hidden problems among the items including larger than needed item amounts in the storage and risks coming from shortage situations.
Item optimization projects collect the history data of stock item usage from the storage CMS. In order to create approximate calculations based on the history data it should include a sufficient number of storage visits per each stock item. The possible flaws in the data are compensated by performing an overview for the optimization results. The overview is focused on the items that show in the optimization results that the current storage strategy (item reorder point and order size) does not fill the required service rate requirement (probability that the storage client gets all the needed spare parts from the storage).
- Project goals:
- Locating stock items that contain risks in their current storage strategies and to correct these strategies in a cost-optimal way
- Locating stock items that has the potential to decrease their overall storing costs (lower stock levels, larger order sizes)
- Project phases:
- Transferring stock item history data from storage database to Excel documents
- Optimizing stock item storage strategies in StockOptim software
- Reviewing the optimization results together with the storage personnel and concentrating on the possibly located problematic storage strategies
- Changing the problematic stock item storage strategies to the storage system
- The reviewing process takes into account that the required service rate can be lowered with some items, or the service rate value calculated by StockOptim from the item usage data is too low compared to the reality, if:
- Item is non-critical and it is considered acceptable that the storage cannot serve all the storage clients perfectly (if item ABC classification is used, it might be considered to lower the current classification)
- Item is usually taken from the storage by a storage client as a larger amount as is needed, and some of the items are stored to some unofficial local storage that cannot be seen in the system (true service rate is higher that the calculated one)
- Item is ordered from the suppliers in different and varying order sizes than what the official storage strategy requires as the 'order size' input (true service rate is higher than the calculated one)