Event Logic Modeling and Analysis Software
Ramentor – ELMAS
Event Logic Modeling and Analysis Software (ELMAS) has been developed for modeling, analysis and optimization of systems' dependability and costs during their whole life cycle. ELMAS can be used, for example, to compare design alternatives, to estimate the return of investment time, and to optimize maintenance of the system. With a user-friendly graphical user interface and efficient simulation algorithms ELMAS is a powerful tool for comprehensive risk assessment and uncertainty management.
Key benefitsKey benefits of ELMAS software
- Modeling systems and subsystems, and predicting life cycle costs (LCC) and resource needs
- Utilizing existing failure data and expert knowledge for system optimization
- Possible to optimize system reliability, availability, maintenance actions and costs already in the design phase
- Improves customer satisfaction
- quick problem solving
- preventing failures from reappearing
- defining dependability requirements (subcontracts, investments)
- Improves productivity and efficiency
- by knowing the causes of problems they can be solved in a preventive manner
- more resources will be available when planning everything right with the first try
- More effective data collection
- Systematic operations model
Risk assessment and RAMS
ELMAS – Risk assessment and RAMS

RAMS = Reliability, Availability, Maintainability, Safety
ModelingModeling

Analyzing
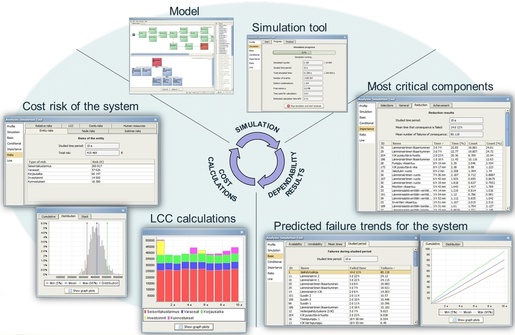
Analyzing function allows defining predictions for e.g. component failure tendencies, most significant failure causes and cost risks coming from these failure events. Result analyzing gives important information about the behavior of the whole system. The aim of the analysis is to locate the methods that can improve the reliability and availability of the overall process as cost-effectively as possible.
OptimizingOptimizing

Reporting
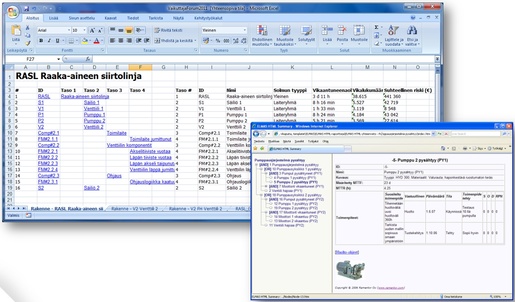
- ELMAS software offers various ways for creating reports:
- HTML report: Active report of the model and the attached data opened with a web browser.
- Excel report: Compact presentation of the model and the attached data. Works also as an interface when importing data from Excel to ELMAS.
- Table summary: Internal table of ELMAS that is typically used for checking, inputting and copying input data.
- FMEA table: Internal FMEA table of ELMAS that can also be exported to Excel.
- Actions report: Table-based summary of the planned actions. Possibility also to export to Excel.
Demo video – ELMAS Process Analysis
StockOptim
Optimizing stock levels and storage costs
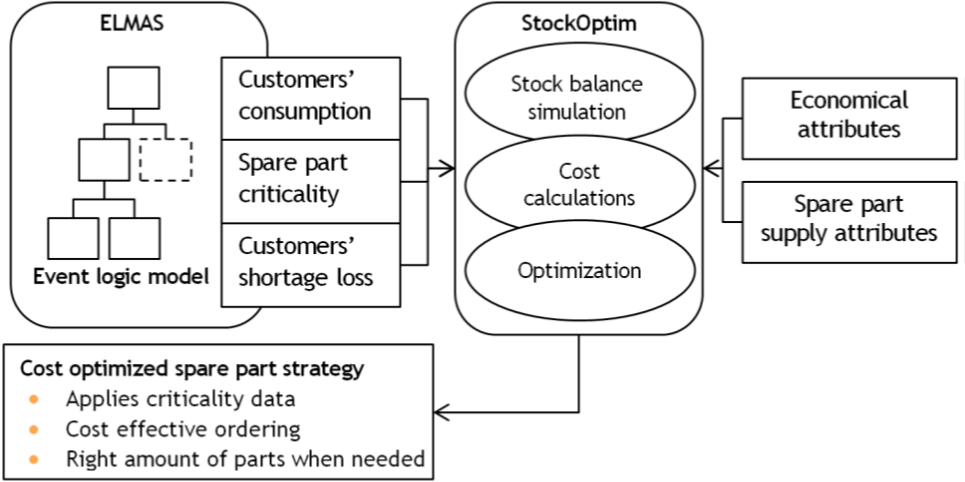
Key benefits of StockOptim software
- Significantly reducing the capital costs coming from storing
- Provides reliable information about storing due to the fact that all the costs connected to it are taken into account
- Provides optimum values for the reorder point, order size and preorder time of stock item
- Possibility to focus on the spare part availability of critical equipment
- Helps developing new cost-effective storing solutions
- Helps comparing different suppliers
- Provides a tool for continuously developing dependability and storage management